
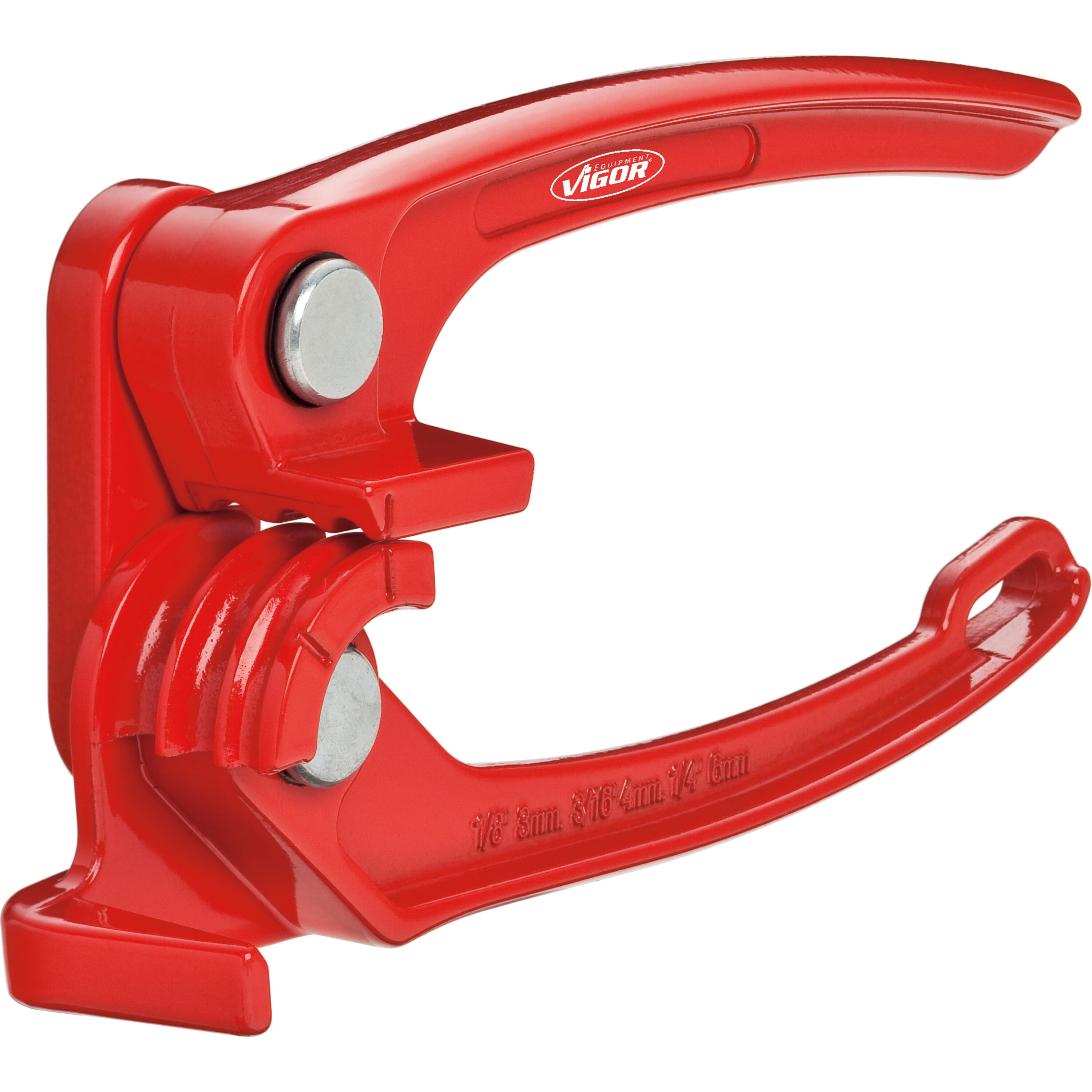
With its machines, it offers both the highest quality for precise results and impressive innovations for special requirements. For all these projects, Profile Bending Technology AG takes a pioneering position.
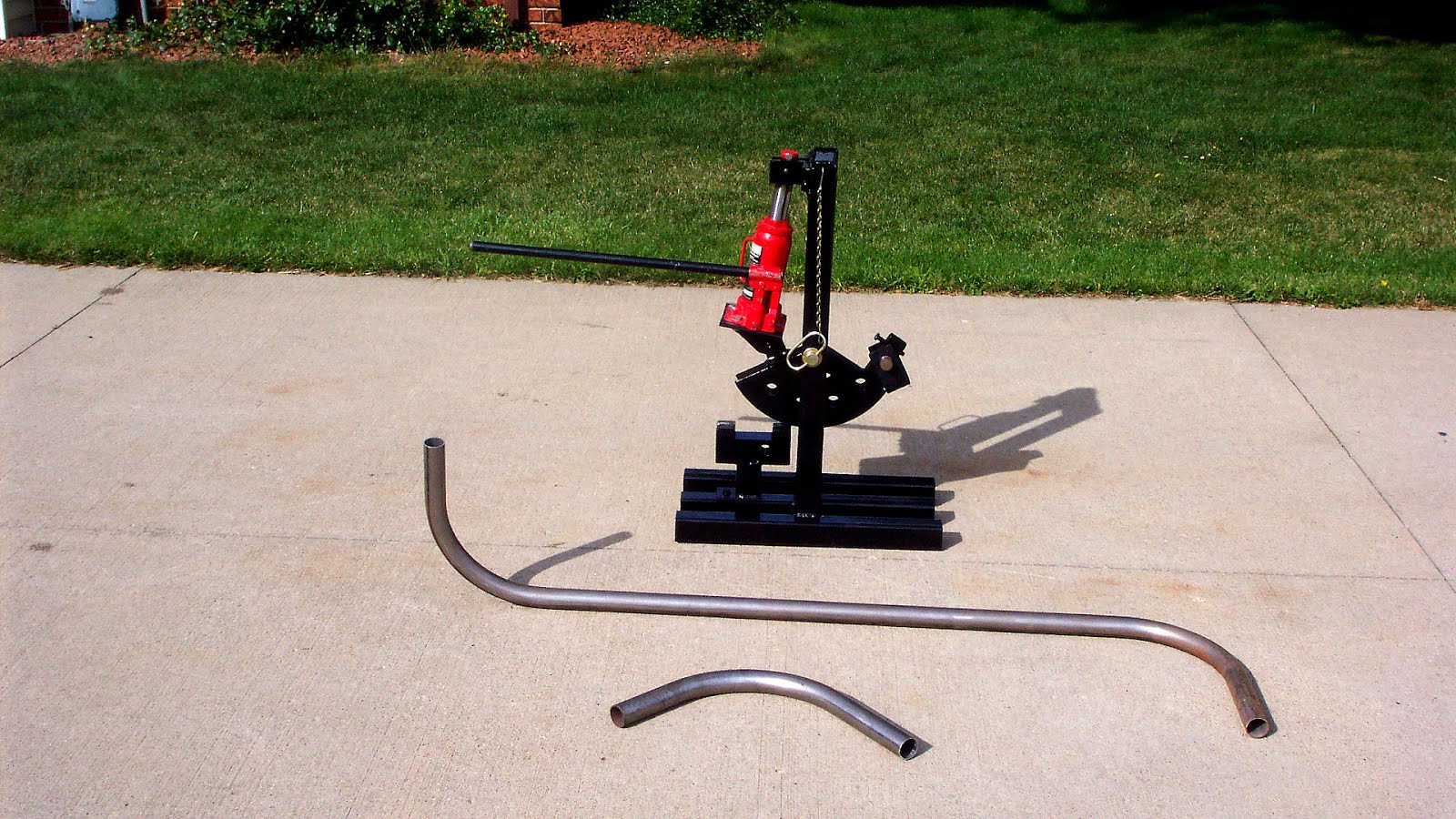

It handles both the simplest bending processes and the complex shaping of large workpieces, whether aluminium, copper or stainless steel. As a common variant, the hydraulic tube bending machine in particular is common in almost every industry. For example, in vehicle construction, materials handling or even in the aerospace industry - the bending of profiles is indispensable in many respects. In these cases, it is necessary to reduce the radius of the tools so that they have the required shape after bending.Small machines and larger systems for bending tubes are part of the equipment of many companies from all kinds of industries. There will be a significant increase occurring primarily in relatively large radius bends ( "D of bend > 4") and during the bending of incredibly stiff materials. Sometimes the radius of the bend will grow over the tooling radius as an effect of the springback defect. The real defect of springback is when the tube is deformed after it returns back. This occurs when it is necessary to bend with a greater angle of bend than is necessary (so-called overbending). This is how the tube will spring back a few degrees in the direction of the bend when released from the tools. It is necessary of course to differentiate ANGULAR SPRINGBACK from RADIAL GROWTH. One common defect is the change in the radius of the bend and the change in the angle of the bend after the end of a bend due to springback. In essence, all are only theoretical and neglect external influences. The calculation for the thickness of the walls on the outer radius for the bending depends on many relationships. The materials of the tube and the equipment used should also be considered. The parameters of the tube bending are crucial (OD, CLR, WT), but there is also a significant impact from the tools and how they are set up. There are many other factors which can lead to the thinning of the walls during a bend. It is very effective to reduce the thinning of the walls with a so-called Booster, which is essentially just extra pressure that pushes on the tube in the direction of the bend and reduces the tension on the inner diameter of the bend. However, you can greatly decrease the amount of thinning on the outer radius by selecting the right choice of tools and setting them up properly.
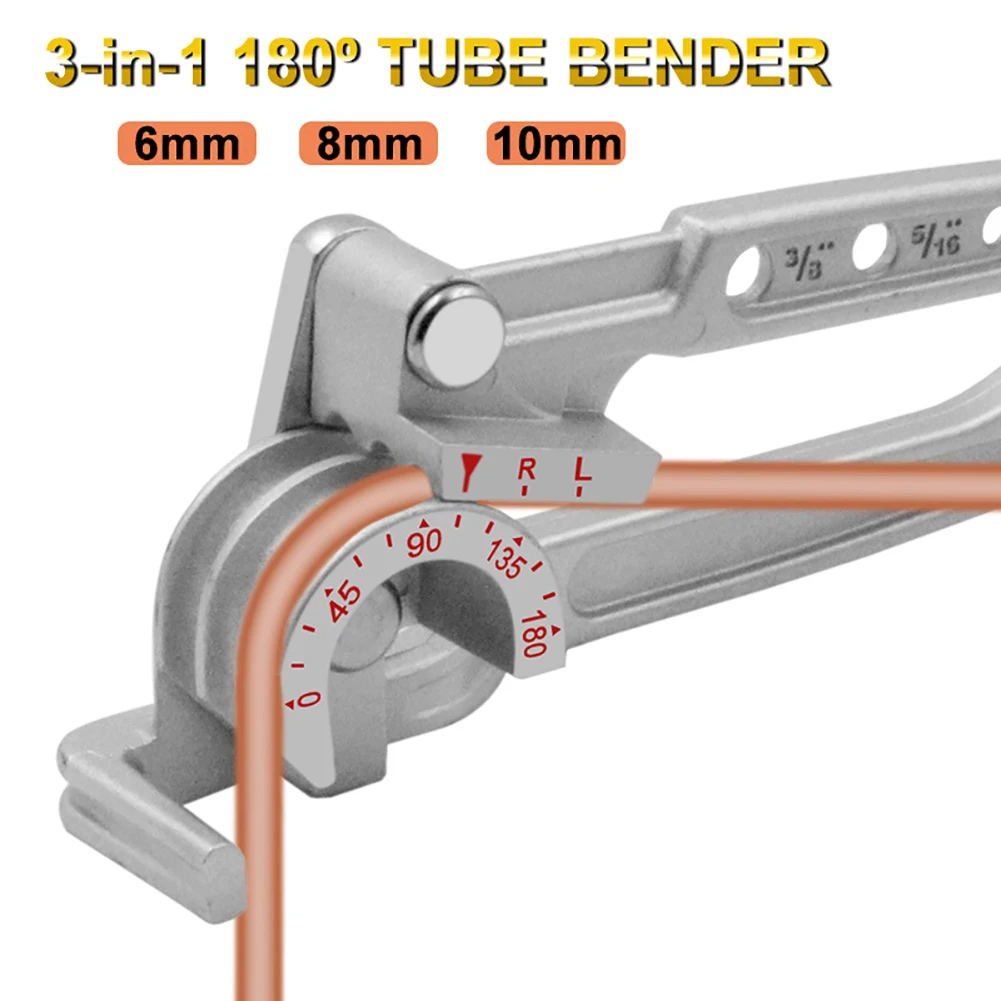
The thinning of the walls on the outer side of the radius of the bend naturally occurs when you are bending tubes. Reduction or limitation of wrinkling can be achieved by properly setting up the appropriate mandrel and wiper die. It is due to pressing forces caused during bending. This is where the stability of the walls is lost on the inner radius of the bend. The flattening can be monitored by using the coefficient of ovalness: Flattening of the cross-section of the tubeįlattening of the cross-section of the tubes is caused by the distribution forces through the bend and can be greatly reduced by using the appropriate inner insert (mandrel) and setting them up properly.
